Valves are essential components in various industries, including oil and gas, chemical processing, and power generation. One type of valve that has gained popularity over the years is the floating valve. Unlike other valves, a floating valve is not attached to the valve body, allowing it to move freely and adjust to changes in pressure. In this article, we'll discuss the benefits and applications of floating valves.
What is a Floating Valve?
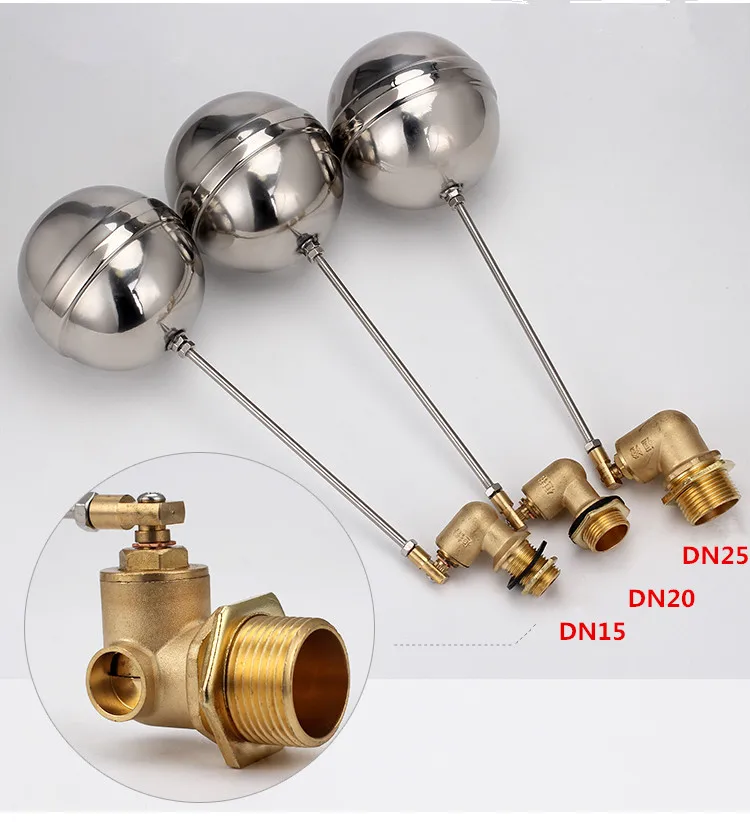
A floating valve, also known as a floating ball valve or floating seat valve, is a type of quarter-turn valve. It consists of a ball with a hole in the middle and two seats, one upstream and one downstream of the ball.
The ball is held in place by a stem that passes through the top of the valve body and is connected to an actuator. The seats are designed to seal against the ball when the valve is closed, preventing fluid from flowing through. When the valve is open, the ball rotates, aligning the hole with the upstream and downstream ports, allowing fluid to flow through.
Benefits of Floating Valves
Floating valves offer several benefits over other types of valves, including:
1. Self-Adjusting Seat

One of the main benefits of a floating valve is that it has a self-adjusting seat. Because the ball in a floating valve is not attached to the valve body, it can move freely. When the valve is closed, the ball presses against the downstream seat, creating a tight seal. This allows the valve to compensate for changes in pressure, temperature, and flow, ensuring a tight seal and preventing leakage.
2. Low Torque
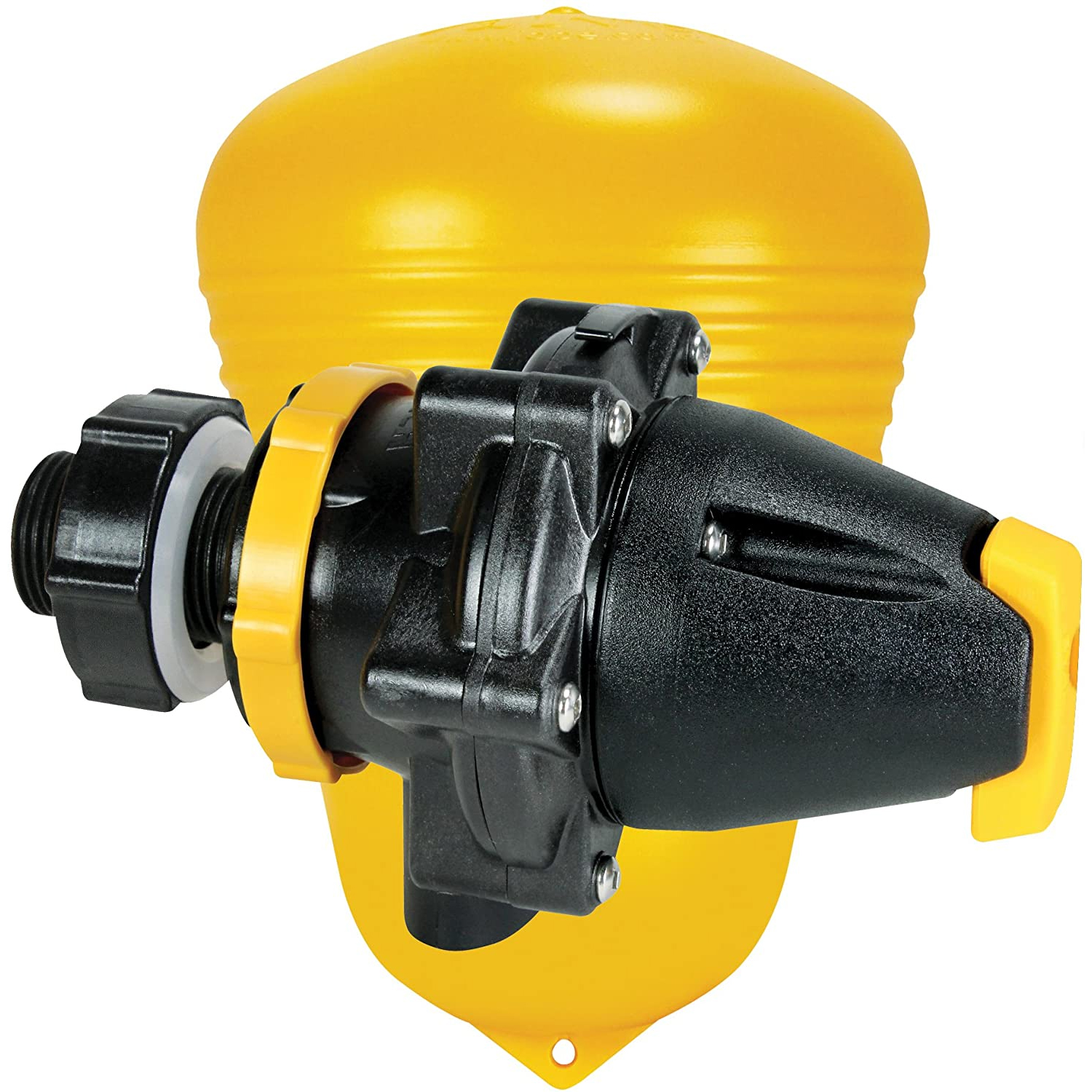
Another benefit of a floating valve is that it has low torque requirements. Because the ball in a floating valve is not attached to the valve body, it requires less torque to operate. This makes floating valves ideal for applications where high torque requirements are impractical or where there are space constraints.
3. Easy Maintenance
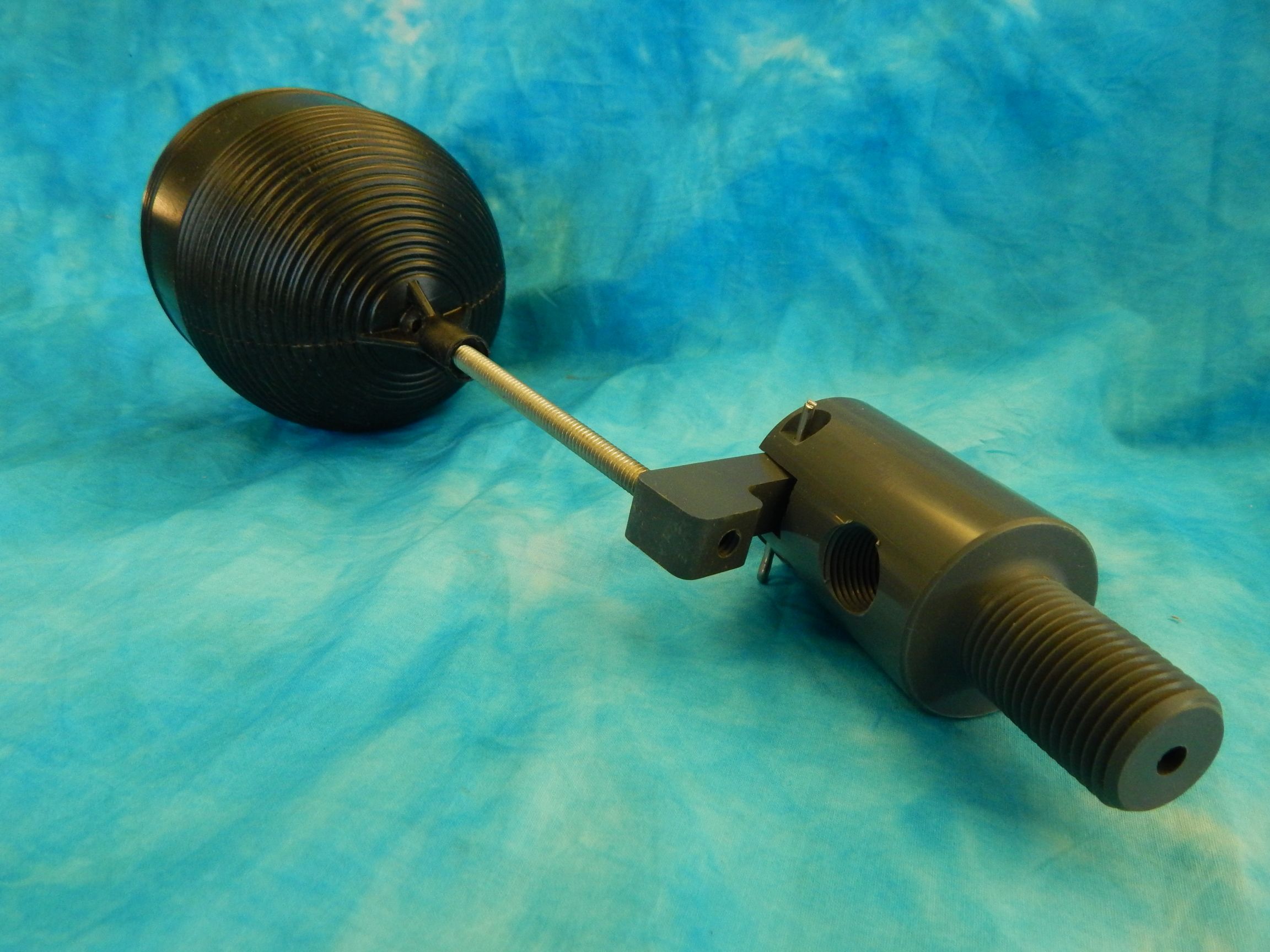
Floating valves are also easy to maintain. Because the ball in a floating valve is not attached to the valve body, it can be easily removed for cleaning or replacement. This reduces downtime and maintenance costs, making floating valves a cost-effective choice for many applications.
Applications of Floating Valves
Floating valves are used in a wide range of applications, including:
1. Oil and Gas Industry
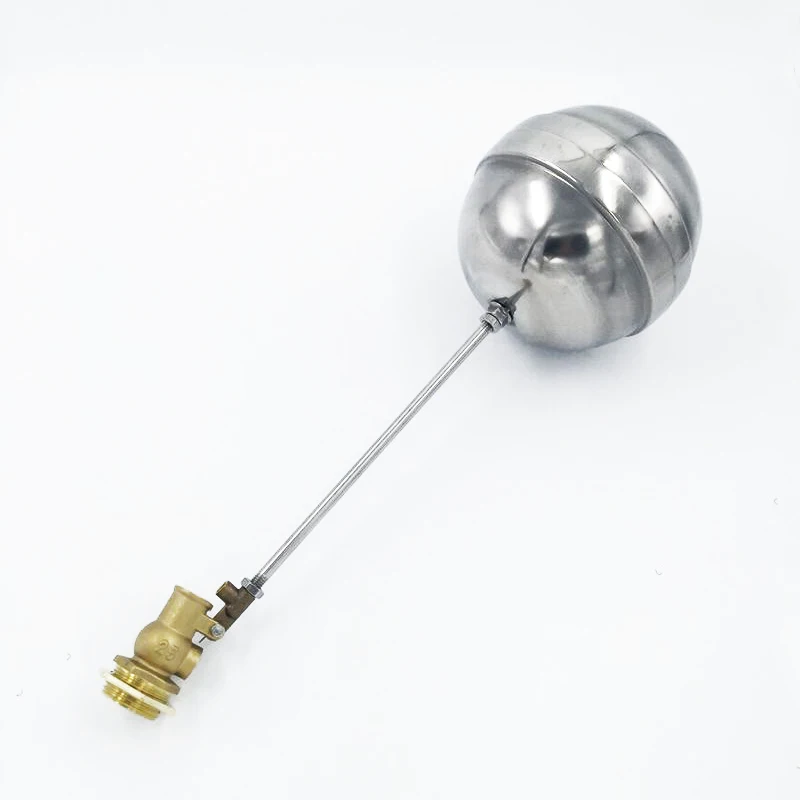
Floating valves are commonly used in the oil and gas industry, where they are used to regulate the flow of crude oil, natural gas, and other fluids. Because of their self-adjusting seat, floating valves are ideal for high-pressure applications and can withstand harsh operating conditions.
2. Chemical Processing
Floating valves are also used in chemical processing applications, where they are used to control the flow of chemicals and other fluids. Because of their easy maintenance and low torque requirements, floating valves are ideal for applications where frequent maintenance is required.
3. Power Generation
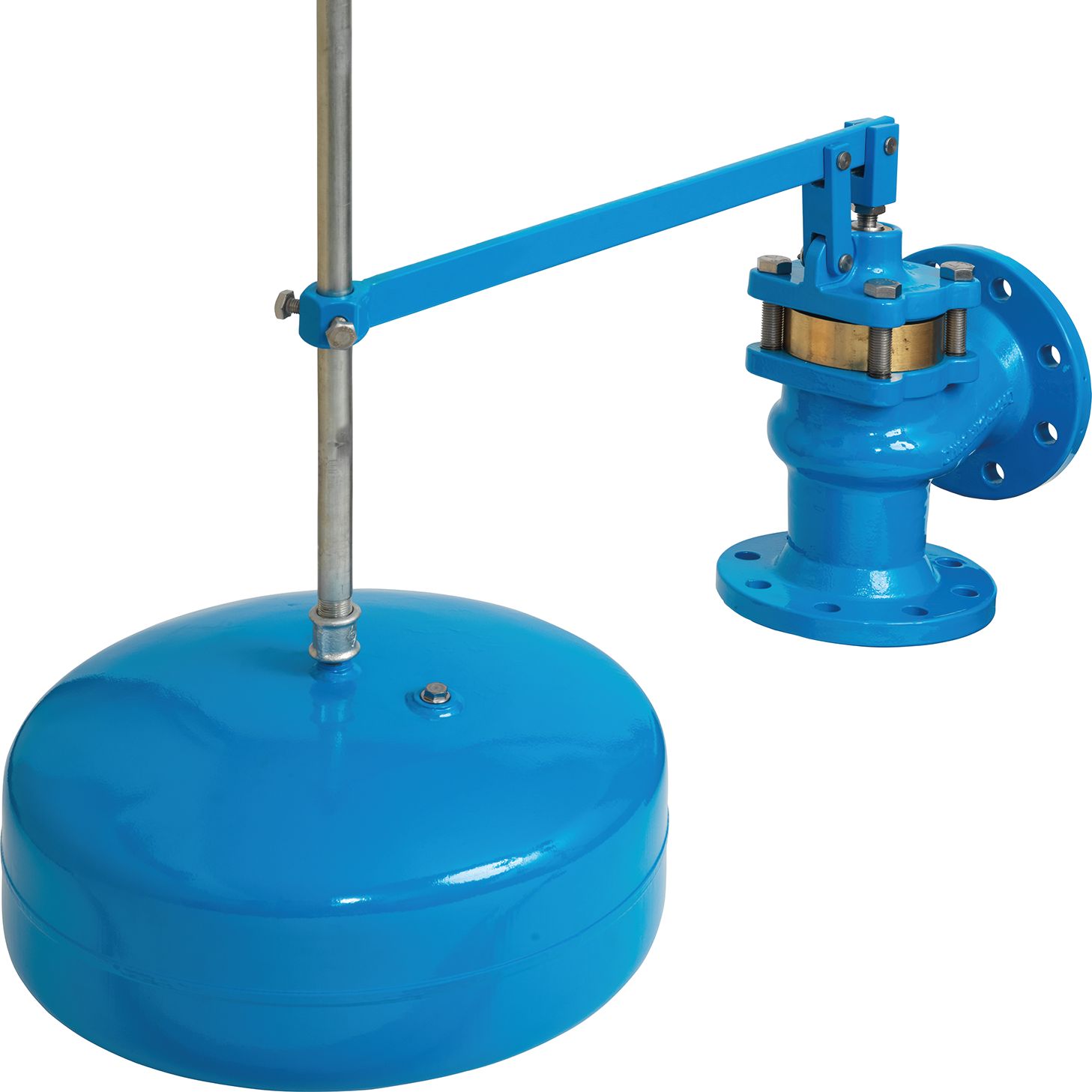
Floating valves are also used in power generation applications, where they are used to regulate the flow of steam and other fluids in boilers and turbines. Because of their self-adjusting seat and low torque requirements, floating valves are ideal for high-temperature and high-pressure applications.
Conclusion
Floating valves are essential components in various industries and offer several benefits over other types of valves. They have a self-adjusting seat, low torque requirements, and are easy to maintain, making them ideal for high-pressure, high-temperature, and harsh operating conditions. If you're looking for a reliable and cost-effective valve, consider a floating valve.